1、 Electrolytic copper foil technological process
Electrolytic copper foil is made by using a cathode roller to precipitate copper cations on the cathode roller surface, which is removed and then surface treated.
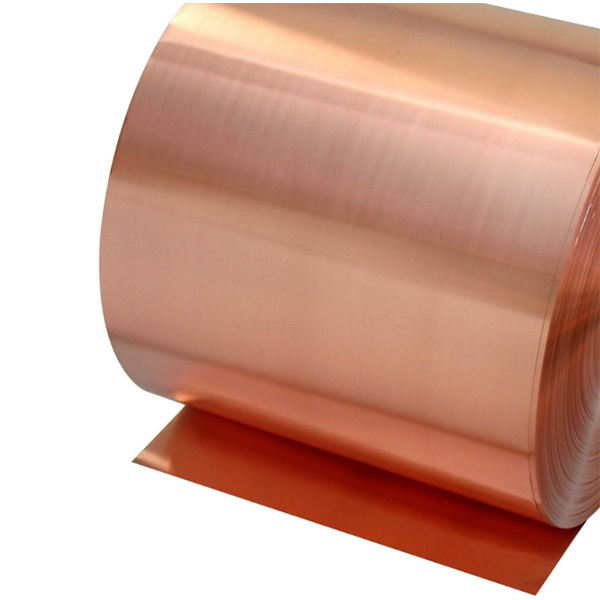
At present, most countries in the world Electrolytic copper foil production The roller type continuous electrolysis method is adopted, which consists of two major parts, namely, the production process of raw foil (or wool foil) and the surface treatment process, namely: copper melting - electrolysis - surface treatment (pickling treatment, roughening treatment).
There are three steps in the surface treatment process: the first step is roughening to further improve the surface structure of the wool foil and improve its adhesion; The second step is electroplating brass or zinc to form an isolation layer to prevent the substrate from being polluted; The third step is zinc plating or nickel, tin, etc. to form an anti oxidation layer.
2. Main equipment for electrolytic copper foil
The equipment is simple in structure and consists of dissolving tank, electroforming (stripping) tank, processor, slitter, coating machine, furnace, shear and coiler.
The dissolving tank dissolves waste copper in sulfuric acid solution;
Electroforming (dissolution) tank stores electrolyte, in which copper ions are electrodeposited on the surface of cathode roll to form copper foil;
The copper foil stripped from the cathode roller by the processor is washed and dried.
Slitter trimming or slitting;
The coating machine is a surface treatment device for surface coating.
3. Characteristics of electrolytic copper foil
The thickness of electrolytic copper foil is 0.14-0.009mm, and 0.018mm and 0.035mm are common.
Electrolytic copper foil is pure copper foil with high copper content and good conductivity, but its quality and density are inferior Calendered copper foil 。 The chemical composition is uniform, the size and allowable deviation are small, and the surface is free of pinholes, wrinkles and other defects. The special property of electrolytic copper foil is that its surface is rough, which can be bonded. After surface treatment, it has a certain strength, and has a strong resistance to stripping, oxidation and discoloration.
4. Application of electrolytic copper foil
Electrolytic copper foil is widely used in PCB manufacturing industry due to its low production cost. However, on flexible moving lines, such as the flip connection of mobile phones, cameras and computers, photocopiers, intelligent machine running parts and other moving lines, electrolytic copper foil is deposited. The structure and properties are essentially different from the processing structure, and the bending resistance is far inferior to the calendered copper foil.
In the past, electrolytic copper foil was mainly used in the construction industry as the inlay decoration of doors, windows and walls; In harsh environment, it can be used as shielding protective cover of radio equipment, coaxial cable shell, etc. At present, the vast majority of electrolytic copper foil produced worldwide is used to manufacture printed circuit boards, flexible bus bars, high-frequency bus bars, heat collectors, etc.
5. Factors affecting the quality of electrolytic copper foil
The main link affecting the thickness of electrolytic copper foil is the forming process of wool foil. The thickness of copper foil is controlled by the composition of electrolyte, current density of cathode roll and rotating speed of cathode roll (electrolysis time). In addition, the factors that affect the peak valley shape of the rough surface and its uniformity during the formation of the rough surface are mainly the surface roughness of the cathode roll and the uniformity of the current density. The factors affecting the porosity of copper foil include whether there are pinholes or dust particles on the surface of cathode roll.
The factors affecting the mechanical properties and electrical conductivity of copper foil mainly include the purity of electrolyte, temperature and crystallization rate. In the process of surface treatment, the factors that affect the size, composition and distribution of coarsening benefits, peel strength, whether there is substrate pollution, heat resistance, oxidation resistance and other characteristics are mainly the treatment methods and process conditions.
The effect of mechanical roughening is poor for copper foil below 0.035mm, and the effect of immersion or spray or corrosion treatment is good.